Valero Energy - Acid Settler Vessel
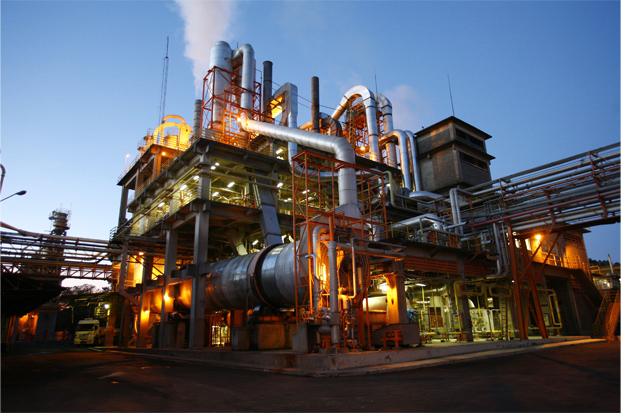
In 2008, Site Heat - treatment Services was awarded a major contract for the supply of heat treatment engineering services for heat treatment on an Acid Settler Vessel at Valero Energy Limited Pembroke Refinery following an initial feasibility study. The heat treatment requirement was associated with the installation of new internal tray ring supports and nozzle modifications on the carbon steel vessel, (6.8m diameter, 47mm wall thickness).
The extent of the heating requirement was such that an external electrical resistance heating system was fitted over a 5.6m vertical length and comprised some 384 ceramic pads fitted to the shell, 160 pads fitted to the nozzles and a further 60 pads to internal support attachments. This corresponded to a total of some 250 control circuits.
The heat treatments, which involved an initial hydrogen bake-out operation, preheat for welding; hydrogen diffusion after welding and a final post weld heat treatment were successfully completed over a period of approximately 8 weeks entirely in accordance with the requirements of ASME VIII, Division 1.
Why a Monitored Bake-out Operation?
Pre-weld hydrogen bake-out heat treatments are a necessary measure in controlling the level of hydrogen in steel that has been subject to the uptake of diffusible hydrogen during service. During maintenance shutdown on process plant, a pressure vessel or other component that normally operates in conditions where hydrogen is introduced into steel parts, may require repair or design modification by welding in the offending area. The presence of hydrogen may even have led to the growth of existing defects (1) leading to subsequent repair. The incidence of such hydrogen related problems applies in particular to petrochemical plant.
Consequently, the residual hydrogen content in the associated steel plate may need to be lowered before any welding, or other operations such as flame-cutting, can proceed. This requirement arises because of the risk of hydrogen induced cracking during and subsequent to any welding operations. A reduction in hydrogen content can be achieved in the affected area of the plate by a pre-weld heat treatment under controlled conditions - the hydrogen bake-out process. Therefore the measurement of hydrogen flux level before welding permits an estimation of the appropriate heat treatment parameters to be adopted. Furthermore, the reduction in hydrogen flux may be monitored throughout the bakeout operation (which normally would not exceed 450°ree;C) until a low target value is reached. A monitored bake-out brings with it a number of benefits including a reduced risk of weld HAZ cracking (and ensuing repairs). It also provides valuable data leading to an effective control of holding time at the prescribed temperature and, of course, satisfactory results. The time penalty for preparation of monitoring and heating is minimal, having a very limited impact on programme time.